Precision Valve Production with Casting & Forging | VALTEK Shanghai
As a China manufacturer, VALTEK Shanghai specializes in valve production using investment casting (lost wax), and forging to ensure high-quality performance. Our advanced ball valve production processes guarantee precision and durability for demanding industrial applications. With expertise in Shanghai manufacturing, we produce reliable ball valves and control valve solutions, meeting global industry standards. Through strict quality control and advanced techniques, VALTEK Shanghai delivers industrial valves designed for durability and efficiency.
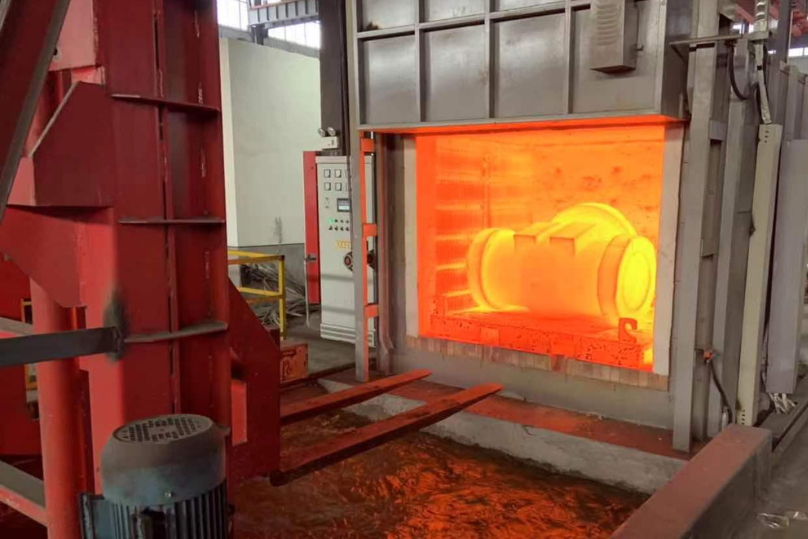
Investment Casting (Lost Wax)
Ball Valve, Valve, Butterfly Valve, Fitting, Flange, Ball, Stem, Castings and more
Carbon Steel (WCB), Stainless Steel
Investment casting (lost wax casting) ensures precise, high-quality valve production with smooth surfaces, tight tolerances, and complex designs. This method enhances valve performance, durability, and sealing while minimizing machining. It supports various metals and alloys, making it ideal for manufacturing stainless steel, carbon steel, and alloy valves for demanding industries.
Precision Casting Process
Investment casting (lost wax casting) follows a series of precision steps to produce high-quality raw castings for valves and industrial components. The process starts with custom injection molding, wax injection, and pattern assembly, followed by dipping and stuccoing to create a ceramic shell. After seasoning and dewaxing, the mold is preheated and filled with molten metal, ensuring precise shape formation and material integrity..
Once the casting solidifies, it undergoes shaking off, sandblasting, and cutting to remove excess material. Acid cleaning and heat treatment further refine surface quality and mechanical properties, enhancing durability and corrosion resistance. A rigorous quality check ensures each casting meets strict industry standards before proceeding to machining and final finishing.
-9jr42d.png)
-5mqp32.png)
Valve Components by Casting
Investment casting is an ideal manufacturing process for producing our valve body, valve end cap, fittings, flanges, valve balls, stems, and other precision castings. This method allows for intricate designs, smooth surfaces, and tight tolerances, ensuring superior performance and minimal machining. With a wide range of material options, including carbon steel (WCB), stainless steel (304, 316, 310), and alloy steel, investment casting provides versatile, high-quality solutions for demanding industrial applications.
Machining & Assembly
After investment casting, valve parts undergo machining and assembly for accuracy and durability. Processes include I.D. machining, stem slot machining, and flow direction turning for precision, flaMachining & Assemblynge turning and drilling for secure installation, and coating for corrosion resistance. Each ball valve undergoes a hydraulic shell test, followed by a quality check to ensure compliance with industry standards.
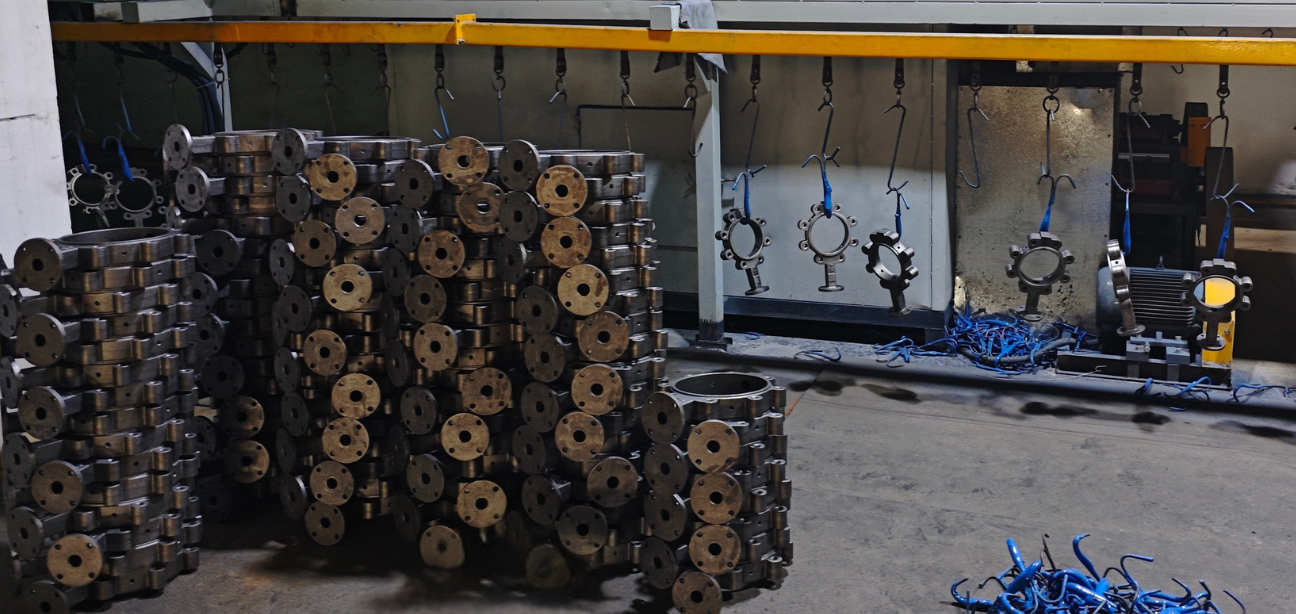
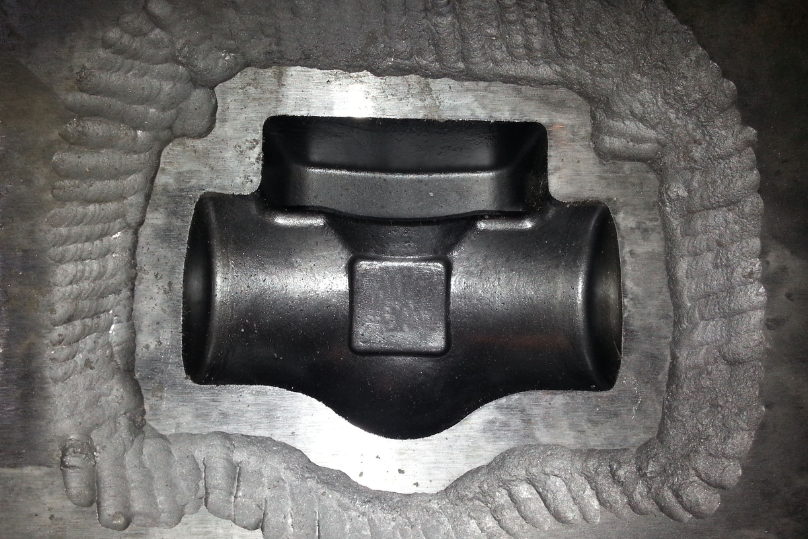
FORGING
Ball Valve, Control Valve, Gate Valve, Globe Valve, Fitting and more
A105N, A182, LF2, F304, F316
Forging production enhances the strength, durability, and reliability of ball valves, industrial valves, and fittings by shaping metal under high pressure and temperature. This process creates a refined grain structure, improving impact resistance, pressure tolerance, and leak tight performance for severe service applications. Forged ball valves offer superior strength and resistance to extreme conditions, making them ideal for oil & gas, chemical, and power industries.
Forging Process
Manufacturing forged ball valves differs from casting, offering greater strength and durability for high pressure and severe service applications. Like casting, the forging process begins with design, where various sizes, pressure ratings and materials are selected to meet specific industry needs. Once the valve design is finalized, the forging process begins by shaping metal components using high pressure and heat. This method refines the metal’s grain structure, improving strength, impact resistance, and pressure tolerance. Valve bodies and components are precisely forged to ensure heavy duty and long lasting performance. During forging, heated metal is compressed and shaped using a die forging machine, applying controlled force to form the exact valve design.
Valve Components by Forging
Forging production is a highly effective method for manufacturing ball valves, control valves, gate valves, globe valves, fittings, and more, ensuring exceptional strength, durability, and performance. This process enables precise shaping and a refined grain structure, enhancing pressure tolerance and mechanical integrity in demanding applications. With a wide range of material options, including A105N, A182, LF2, F304, and F316, forging provides impact strength and reliability. These properties make forged valves and fittings ideal for high pressure, high temperature and critical service conditions in industries such as oil & gas, power generation, and chemical processing.
Machining & Assembly
After the forging process, components undergo precise machining and assembly to ensure optimal performance and durability. This includes flow direction turning, valve body drilling, flange drilling & machining, stem slot machining, and valve end cap machining, all of which refine dimensions and enhance functionality. Once machining is complete, the components proceed to assembly, followed by a hydraulic shell test to verify pressure integrity and sealing performance. To enhance durability and corrosion resistance, a protective coating is applied. A final quality check ensures that each valve meets strict industry standards before shipment.
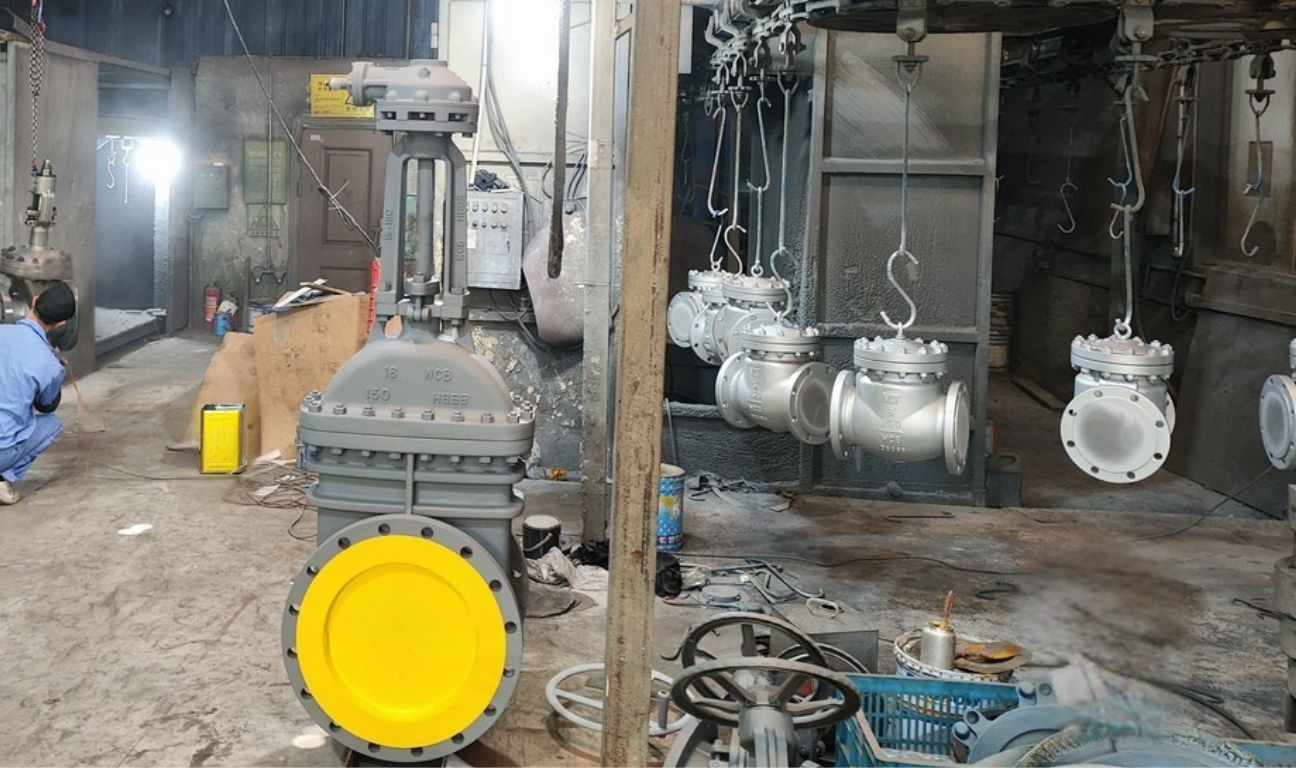
-9d16xd.png)
-egr8rb.png)
-335urd.png)